2025-01-30
Precyzja i tolerancje wymiarowe osiągane w cięciu laserowym blach
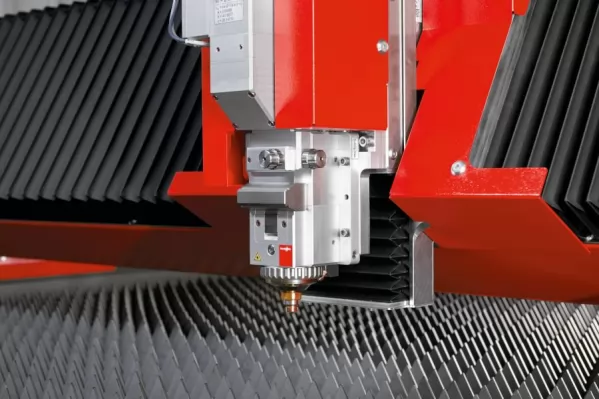
Technologia cięcia laserowego zrewolucjonizowała przemysł obróbki metali, oferując kombinację wysokiej precyzji, powtarzalności i wydajności produkcyjnej, której nie można osiągnąć konwencjonalnymi metodami. W miarę rozwoju tej technologii, precyzja i tolerancje wymiarowe ulegały ciągłemu udoskonaleniu, umożliwiając wykonywanie coraz bardziej złożonych elementów przy jednoczesnym zachowaniu wyjątkowej dokładności. Niniejszy artykuł szczegółowo analizuje kluczowe aspekty precyzji wymiarowej w procesach cięcia laserowego blach, czynniki wpływające na osiągane tolerancje oraz najnowsze osiągnięcia technologiczne w tym zakresie.
Charakterystyka precyzji cięcia laserowego
Podstawowe parametry precyzji
Precyzja cięcia laserowego jest określana przez szereg kluczowych parametrów:
- Dokładność pozycjonowania - określa zdolność systemu do precyzyjnego ustawienia głowicy tnącej w zadanym punkcie przestrzeni roboczej. Nowoczesne systemy CNC oferują dokładność pozycjonowania na poziomie ±0,01 mm.
- Powtarzalność - zdolność maszyny do wielokrotnego osiągania tych samych parametrów wymiarowych podczas seryjnej produkcji. Współczesne lasery przemysłowe charakteryzują się powtarzalnością rzędu ±0,005 mm.
- Szerokość szczeliny cięcia (kerf) - szerokość materiału usuwanego podczas cięcia, typowo w zakresie 0,1-0,5 mm, zależnie od typu lasera, mocy oraz ciętego materiału.
- Prostopadłość krawędzi - odchylenie od idealnego kąta 90° między powierzchnią ciętą a płaszczyzną blachy. Nowoczesne systemy osiągają prostopadłość poniżej 0,05 mm dla blach o grubości do 10 mm.
- Chropowatość powierzchni cięcia - mierzona zazwyczaj parametrem Ra (średnie arytmetyczne odchylenie profilu), osiąga wartości w zakresie 3,2-12,5 μm, zależnie od parametrów procesu.
Porównanie z innymi metodami cięcia
W porównaniu z alternatywnymi metodami cięcia blach, technologia laserowa wyróżnia się pod względem precyzji:
Laser światłowodowy charakteryzuje się dokładnością rzędu ±0,01 mm, przy szerokości szczeliny cięcia 0,1-0,25 mm i chropowatości powierzchni Ra w zakresie 3,2-6,3 μm. Jest to obecnie jedna z najdokładniejszych metod cięcia blach.
Laser CO₂ oferuje dokładność na poziomie ±0,05 mm, z szerokością szczeliny 0,2-0,5 mm i chropowatością powierzchni Ra w przedziale 6,3-12,5 μm. Choć nieco mniej precyzyjny od lasera światłowodowego, nadal zapewnia wysoką jakość cięcia.
Plazma HyDefinition osiąga dokładność około ±0,2 mm, przy szerokości szczeliny 1,5-2,0 mm i relatywnie wysokiej chropowatości powierzchni Ra 12,5-25 μm. Jest to metoda wyraźnie mniej precyzyjna niż technologie laserowe.
Waterjet (cięcie wodą) zapewnia dokładność na poziomie ±0,1 mm, z szerokością szczeliny 0,8-1,2 mm i chropowatością Ra 3,2-6,3 μm, porównywalną z laserami światłowodowymi, jednak przy większej szerokości cięcia.
Wykrawanie CNC charakteryzuje się dokładnością około ±0,05 mm, jednak w przeciwieństwie do metod cięcia termicznego, nie występuje tu zjawisko szczeliny cięcia. Ograniczeniem tej metody jest konieczność stosowania specjalistycznych narzędzi dla różnych kształtów.
Podsumowując, lasery światłowodowe oferują najlepszą kombinację dokładności, wąskiej szczeliny cięcia i niskiej chropowatości powierzchni, co czyni je optymalnym wyborem dla zastosowań wymagających wysokiej precyzji wymiarowej.
Czynniki wpływające na precyzję wymiarową
Parametry lasera i procesu
- Moc wiązki laserowej - wyższa moc umożliwia szybsze cięcie, ale może prowadzić do zwiększenia szerokości szczeliny cięcia oraz większego nagrzewania materiału, co wpływa na ostateczną precyzję.
- Tryb pracy lasera - lasery mogą pracować w trybie ciągłym (CW) lub pulsacyjnym, co ma znaczący wpływ na jakość krawędzi i precyzję wymiarową, szczególnie w przypadku materiałów o dużej grubości.
- Ogniskowanie wiązki - precyzyjne ogniskowanie wiązki oraz utrzymanie optymalnej odległości ogniskowej ma kluczowe znaczenie dla uzyskania wąskiej szczeliny cięcia i wysokiej jakości krawędzi.
- Prędkość cięcia - zbyt wysoka prędkość może prowadzić do niepełnego przecięcia materiału, podczas gdy zbyt niska może powodować nadmierne topienie i pogorszenie jakości krawędzi.
- Gaz technologiczny - rodzaj i ciśnienie gazu pomocniczego (tlen, azot, argon) wpływa na szerokość szczeliny cięcia oraz jakość powierzchni ciętej.
Właściwości materiału
Różne materiały i ich grubości wymagają odmiennych parametrów cięcia dla osiągnięcia optymalnej precyzji:
- Stal niestopowa - cięcie z wykorzystaniem tlenu jako gazu procesowego pozwala na uzyskanie tolerancji wymiarowych rzędu ±0,1 mm dla blach o grubości do 20 mm.
- Stal nierdzewna - cięta zazwyczaj z użyciem azotu, charakteryzuje się tolerancjami wymiarowymi ±0,05 mm dla blach o grubości do 12 mm.
- Aluminium - ze względu na wysoką refleksyjność i przewodność cieplną, tolerancje wymiarowe wynoszą około ±0,1 mm dla blach o grubości do 10 mm.
- Materiały specjalne (miedź, tytan) - wymagają precyzyjnego doboru parametrów, a osiągane tolerancje wymiarowe wahają się w granicach ±0,1-0,2 mm.
Konstrukcja i parametry maszyny
- Sztywność konstrukcji - maszyny o wyższej sztywności zapewniają lepszą stabilność podczas cięcia, co przekłada się na wyższą precyzję wymiarową.
- System napędowy - nowoczesne systemy wykorzystują napędy liniowe o wysokiej dynamice, pozwalające na precyzyjne pozycjonowanie z przyśpieszeniem do 30 m/s² i prędkościami do 180 m/min.
- System sterowania CNC - zaawansowane algorytmy sterowania, kompensacja błędów oraz interpolacja trajektorii wpływają na końcową precyzję wykonywanych elementów.
- System monitorowania procesu - technologie adaptacyjnego sterowania parametrami cięcia w czasie rzeczywistym umożliwiają utrzymanie wysokiej precyzji niezależnie od zmiennych warunków procesu.
Zaawansowane technologie poprawiające precyzję
Innowacyjne rozwiązania laserowe
- Lasery światłowodowe o wysokiej jakości wiązki - charakteryzujące się niskim parametrem BPP (Beam Parameter Product), zapewniają wyjątkowo wąską szczelinę cięcia (poniżej 0,1 mm) i pozwalają na uzyskanie tolerancji wymiarowych ±0,01 mm.
- Technologia adaptacyjnego ogniskowania - automatyczne dostosowanie parametrów ogniskowania w zależności od grubości i rodzaju materiału, zapewniające optymalną jakość cięcia.
- Systemy detekcji przebicia - minimalizujące zniekształcenia termiczne poprzez optymalizację procesu przebijania materiału.
- Inteligentne algorytmy mikrojonizacji - redukujące efekt przegrzewania krawędzi podczas cięcia skomplikowanych kształtów i małych otworów.
Zaawansowane systemy sterowania
- Kompensacja termiczna - systemy uwzględniające rozszerzalność cieplną maszyny i materiału, zapewniające stabilną precyzję wymiarową w zmiennych warunkach temperatury.
- Dynamiczna adaptacja parametrów cięcia - systemy w czasie rzeczywistym dostosowujące parametry procesu do zmian w materiale i geometrii ciętego elementu.
- Zaawansowane algorytmy optymalizacji ścieżki - minimalizujące odkształcenia termiczne poprzez inteligentne sekwencjonowanie operacji cięcia.
- Systemy wizyjne i pomiarowe - umożliwiające weryfikację wymiarową elementów w trakcie procesu produkcyjnego.
Osiągane tolerancje wymiarowe w praktyce przemysłowej
Standardowe tolerancje dla różnych materiałów i grubości
- Blachy cienkie (< 3 mm):
- Stal węglowa: ±0,05 mm
- Stal nierdzewna: ±0,03 mm
- Aluminium: ±0,08 mm
- Blachy średnie (3-8 mm):
- Stal węglowa: ±0,10 mm
- Stal nierdzewna: ±0,08 mm
- Aluminium: ±0,15 mm
- Blachy grube (8-25 mm):
- Stal węglowa: ±0,15 mm
- Stal nierdzewna: ±0,20 mm
- Aluminium: ±0,25 mm
Precyzja wymiarowa dla cech specjalnych
- Małe otwory - dla otworów o średnicy poniżej 5 mm osiągana jest tolerancja w zakresie ±0,05 mm, przy czym minimalny wymiar otworu zależy od grubości blachy (typowo nie mniej niż 0,5 × grubość).
- Ostre narożniki - nowoczesne systemy laserowe umożliwiają wykonywanie narożników z promieniem wewnętrznym rzędu 0,2-0,5 mm, zależnie od grubości materiału.
- Geometria złożona - dla elementów o złożonym kształcie i licznych przejściach geometrycznych tolerancje mogą być utrzymane na poziomie ±0,1 mm dla całego konturu.
Metody kontroli i zapewnienia jakości wymiarowej
Metody pomiarowe
- Systemy CMM (Coordinate Measuring Machine) - pozwalające na precyzyjne pomiary trójwymiarowe z dokładnością do 0,001 mm.
- Systemy wizyjne - umożliwiające szybką weryfikację wymiarową elementów bezpośrednio na maszynie.
- Skanery laserowe 3D - dostarczające kompleksowej informacji o wymiarach i geometrii elementu.
- Profilometry optyczne - służące do analizy mikrogeometrii krawędzi ciętych.
Procedury zapewnienia jakości
- Kalibracja maszyny - regularne procedury kalibracyjne zapewniające utrzymanie deklarowanych parametrów precyzji.
- Próby technologiczne - wykonywanie elementów testowych przed rozpoczęciem produkcji seryjnej.
- Statystyczna kontrola procesu (SPC) - metody statystyczne pozwalające na monitorowanie stabilności procesu i wczesne wykrywanie odchyleń.
- Certyfikacja procesów - zgodność z normami branżowymi, takimi jak ISO 9013 określająca jakość powierzchni ciętych termicznie.
Wyzwania i ograniczenia
Fizyczne ograniczenia precyzji
- Efekty termiczne - odkształcenia i naprężenia indukowane termicznie podczas cięcia, szczególnie istotne dla cienkościennych elementów o złożonej geometrii.
- Refleksyjność materiałów - materiały o wysokiej refleksyjności, jak miedź czy mosiądz, stanowią wyzwanie dla utrzymania wysokiej precyzji cięcia.
- Ograniczenia prędkości - kompromis między produktywnością a precyzją wymiarową, szczególnie istotny przy produkcji masowej.
Sposoby przezwyciężania ograniczeń
- Techniki minimal heat input - zoptymalizowane parametry procesu minimalizujące wprowadzanie ciepła do materiału.
- Zaawansowane algorytmy compensation loop - kompensujące przewidywane odkształcenia termiczne.
- Hybrydowe strategie cięcia - łączące zalety różnych parametrów procesu dla różnych fragmentów elementu.
Przyszłość precyzji w cięciu laserowym
Trendy rozwojowe
- Lasery ultrakrótkoimpulsowe - femtosekundowe lasery umożliwiające cięcie praktycznie bez strefy wpływu ciepła, z niespotykaną dotąd precyzją.
- Systemy AI i machine learning - adaptacyjne algorytmy uczące się optymalnych parametrów dla konkretnych zastosowań.
- Integracja z technologiami przemysłu 4.0 - kompleksowe systemy produkcyjne zapewniające pełną traceability parametrów wymiarowych.
- Digital twin - cyfrowe bliźniaki procesu cięcia, pozwalające na symulację i optymalizację parametrów przed fizycznym wykonaniem elementu.
Podsumowanie
Precyzja i tolerancje wymiarowe osiągane w procesie cięcia laserowego blach stanowią jeden z głównych atutów tej technologii. Wraz z rozwojem źródeł laserowych, systemów sterowania oraz metod diagnostycznych, możliwości w zakresie dokładności wymiarowej stale się poszerzają. Współczesne systemy laserowe umożliwiają realizację wymagających projektów inżynierskich z tolerancjami wymiarowymi na poziomie dziesiątych, a nawet setnych części milimetra, otwierając nowe możliwości dla przemysłu precyzyjnego.
Kluczowym czynnikiem sukcesu w osiąganiu wysokiej precyzji wymiarowej pozostaje kompleksowe podejście uwzględniające właściwości obrabianego materiału, parametry procesu, konstrukcję maszyny oraz zaawansowane techniki sterowania i monitorowania. Tylko zintegrowane podejście do tych aspektów pozwala na pełne wykorzystanie potencjału technologii cięcia laserowego w kontekście dokładności wymiarowej wykonywanych elementów.
«powrót